ORIFICIOS DIFUSORES en álabes de turbinas.
\ Solución EDM a medida: Orificios difusores en álabes de turbinas.
La estrategia de ONA en el sector aeronáutico pasa, en gran parte, por proporcionar a las empresas soluciones personalizadas de alto valor añadido. Un ejemplo de ello es el desarrollo de una aplicación a medida para un importante fabricante de componentes de alta calidad en las industrias aeroespacial y energética. Este requisito de calidad resultó clave para ellos a la hora de decantarse por ONA.
El cliente necesitaba una solución para realizar el tallado de orificios difusores en álabes de turbinas. Estos orificios cumplen un papel relevante de ventilación y refrigeración. Un mal desempeño de esta función podría aumentar la temperatura de entrada del aire en la turbina y acabar afectando a su eficiencia y durabilidad. En una turbina para la generación de energía se produciría menos energía, y en una turbina para propulsión (como la de un avión) se consumiría más combustible. Por otro lado, las altas temperaturas podrían acabar dañando también a los propios álabes del compresor.
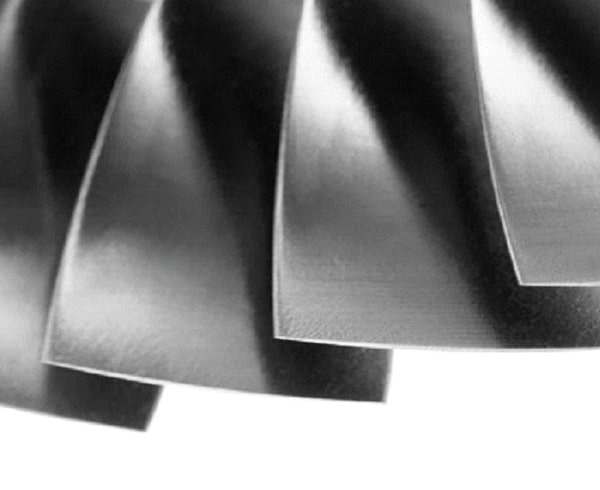
Normalmente los orificios en los álabes se realizan con nuestra maquinaria FAST HOLE (FH), tecnología especializada que permite una mayor velocidad de mecanizado. Sin embargo, las elevadas exigencias de precisión y de calidad del fabricante para la realización de los orificios (con diferentes formas geométricas: cónicos, trapezoidales, etc.) no podían alcanzarse por medio de los equipos FH, lo que le llevó a solicitar a ONA una solución específica para este problema.
La propuesta de nuestros ingenieros fue el desarrollo de una aplicación que sumara las capacidades de dos tecnologías EDM: FAST HOLE y electroerosión por penetración. Primero se hacen unos orificios cilíndricos en la pieza por medio de una máquina FH y, a continuación, y empleando una máquina ONA IRIS6 (recorridos del eje X-Y-Z: 1000 x 750 x 650 mm; con mesa giratoria de 2 ejes y electrodo de cobre), se realizan en esos mismos orificios otros con las formas geométricas deseadas. Algunos de estos orificios pueden tener un eje que no es paralelo al eje del primer agujero.
¿Cómo lo hicimos?
Una dificultad a tener en cuenta a la hora de ejecutar este proyecto fue el contexto mundial de aquel momento. Nos encontrábamos en plena pandemia a causa del Covid, lo que imposibilitaba las reuniones presenciales entre el equipo de ONA y el cliente. Este reto fue superado gracias a la excelente colaboración entre los diferentes departamentos ONA y a nuestras capacidades digitales, culminando con la presentación de una oferta telemática al cliente final.
En este escenario, y para que el cliente pudiera apreciar con detalle cómo se iba a resolver la aplicación (todo el proceso de electroerosión de los difusores), se realizó una simulación completa en nuestro CAD/CAM. Las etapas en el desarrollo de esta simulación fueron las siguientes:
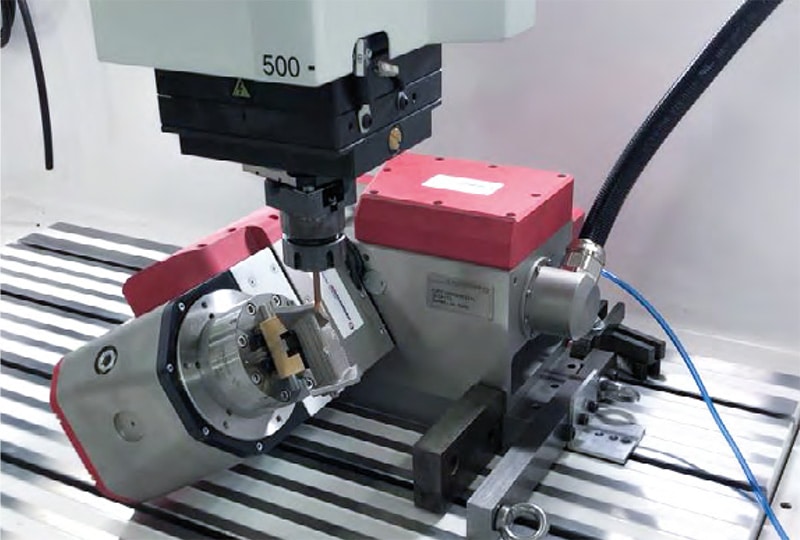
-
Plan de viabilidad y calidad.
Se comenzó realizando un plan de viabilidad y calidad final para comprobar si se podía realizar la prueba con una máquina de ONA. Dicho plan se puso en marcha en una máquina del showroom.
-
Idoneidad de utilizar la ONA IRIS6
Una de las conclusiones de ese estudio previo de viabilidad era la idoneidad de utilizar la máquina ONA IRIS6 debido a las propias características del proyecto: tamaño de las piezas y necesidad de mesa giratoria para poder realizar todos los agujeros y poder ir girando la pieza. En el caso de electrodo, se decidió realizarlo en cobre para conseguir una mayor calidad de acabado.
-
Oferta en video
Dada la situación de pandemia, limitaciones y el interés mostrado por parte del cliente para avanzar en el proyecto, desde ONA realizamos una oferta en video comprometiéndonos con el resultado final de la pieza.
-
Ver y enlazar con CAD-CAM el nuevo CNC.
El cliente solicitó ver el nuevo CNC y cómo se enlaza con el CAD-CAM. Desde ONA, trabajamos en ambos para obtener el mejor ‘matching’ entre ellos, consiguiendo que la pieza “ideal” realizada en CAD-CAM se ejecute en el CNC de la máquina y el resultado final sea idéntico a lo planteado. En este caso, era muy importante localizar los agujeros ya realizados, tener claras las coordenadas en real y que la máquina realizara la ejecución en el punto exacto. El set-up de la pieza es clave, así como saberla ubicar respecto a un punto, ya que la forma de las piezas era muy compleja.
-
Programación con ONA Script
Finalmente, se realizó una programación con ONA Script en el que se genera un flujo para que la máquina realice todo el proceso.
En el caso de este trabajo se trataba de un proyecto ‘llave en mano’ que estuvo en todo momento protagonizado por un elevado nivel de colaboración con el cliente. Esto facilitó alcanzar con éxito el objetivo final: llegar a una fabricación de pieza directa.
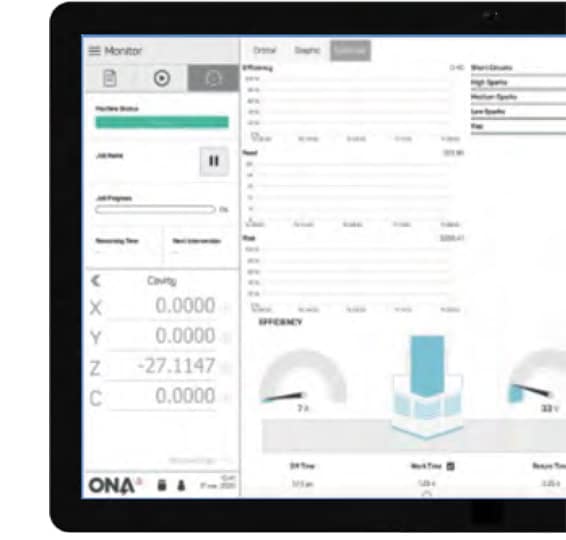
Conclusiones
Con todo este trabajo y estudios previos se pudo entregar al cliente una máquina de penetración totalmente personalizada y programada de acuerdo a sus necesidades específicas para el tallado de difusores de geometría compleja en álabes de turbinas. Nuestra solución ‘llave en mano’ tuvo, además, un coste inferior a otras alternativas del mercado, tal y como nos trasladó el propio cliente.
La máquina ONA IRIS6 lleva incorporado un generador digital inteligente que constituye una innovación tecnológica única en electroerosión. Es un 30% más potente que el resto de generadores más avanzados. Puede alcanzar hasta los 400 amperios, cuatro veces más potencia que el estándar, y está diseñado para optimizar la erosión al controlar el aporte de energía de cada descarga, lo que reduce el desgaste de los electrodos hasta en un 500%.
Las empresas aeronáuticas más importantes del mundo ya utilizan máquinas ONA en sus procesos, y nuestro objetivo es seguir innovando y creciendo en un sector en el que la electroerosión va a tener cada vez más protagonismo. Si hasta hace no mucho eran unas pocas las aplicaciones que se fabricaban con EDM, en la actualidad, y gracias al gran salto tecnológico dado con los nuevos generadores digitales, el mecanizado por descarga eléctrica se ha convertido en una tecnología preferente para la producción de piezas críticas como impellers, IBRs, OGVs, discos de turbinas o cámaras de combustión, entre otras.