Caso práctico: La electroerosión por hilo como alternativa para el mecanizado de ranuras de disco de turbina para el sector aeronáutico.
ONA ha llevado a cabo un estudio para analizar el proceso de electroerosión de corte por hilo (WEDM) como alternativa al mecanizado convencional (brochado) de ranuras de disco de turbina para el sector aeronáutico.
\ La Electroerosión para el mecanizado de ranuras de disco de turbina
Ser líder del sector de la Electroerosión solo puede ser posible si hay un trabajo continuo de investigación de nuevas tecnologías y aplicaciones para dar soluciones avanzadas adaptadas a las necesidades de los clientes. ONA es un ejemplo claro de empresa orientada a la innovación. Sus 70 años de trayectoria aportando mejoras tecnologías a la electroerosión lo avalan.
De acuerdo a esta filosofía, la compañía vasca ha llevado a cabo un estudio para analizar el proceso de electroerosión de corte por hilo (WEDM) como alternativa al mecanizado convencional (brochado) de ranuras de disco de turbina para el sector aeronáutico. De hecho, la electroerosión por hilo de ranuras de disco de turbina podría convertirse en una opción industrial viable al brochado en el futuro.
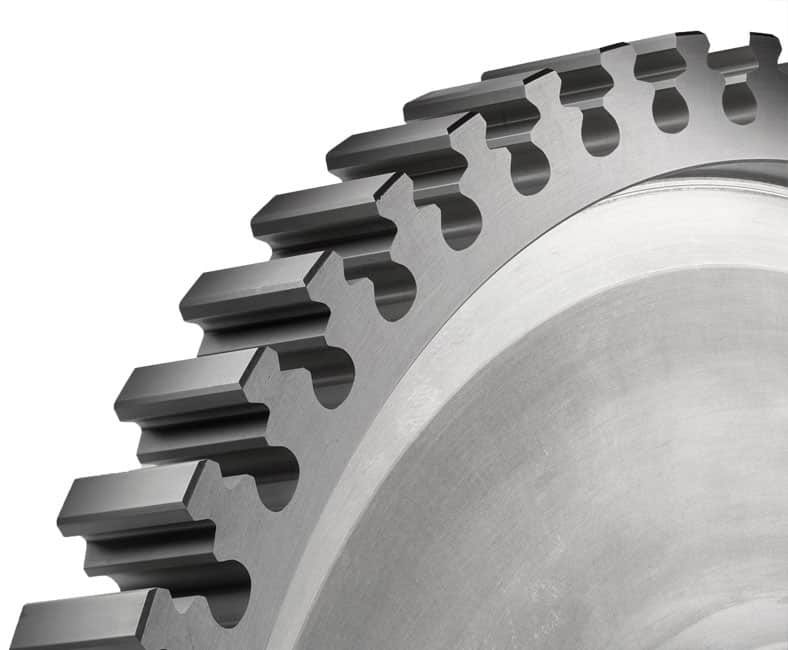
\ Suposición y método
En su investigación, ONA ha comparado el proceso de electroerosión con los mecanizados más tradicionales como son el brochado y fresado. Como puntos clave de la investigación, ONA compara parámetros como los requisitos de integridad superficial, precisión y tiempo de mecanizado de los ranuras de inserción de álabes.
Para la prueba se ha cortado un disco de turbina con las siguientes características:
- Material: Inconel 718
- Diámetro externo: 350 mm.
- 28 ranuras.
- Ranuras de disco de turbina en ángulo de 30 grados.
- 82 mm de espesor.
- Tolerancia de perfil 0.01 mm.
- Tolerancia de posicionamiento angular radial 0.08 mm.
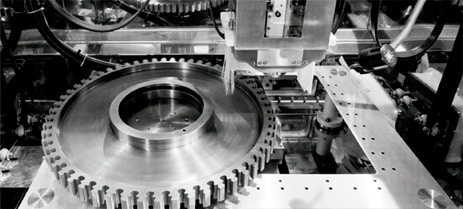
El objetivo de la investigación es cortar mediante la tecnología de electroerosión de corte por hilo los dientes del firtree de la turbina cumpliendo los requisitos de tolerancias y, de esta manera, analizar la siguiente información:
- Tiempo de desbaste de un perfil completo.
- Tiempo de acabado de un perfil completo.
- Tiempo total de erosión de un perfil completo.
- Tiempo total del desbaste del disco de turbina (incluyendo el tiempo de preparación).
- Tiempo total del acabado del disco de turbina (incluyendo el tiempo de preparación).
- Tiempo total de mecanizado (incluyendo el tiempo de configuración).
- Capacidad de arranque de material MMR (mm2/min).
- Espesor de la capa de material refundido.
\ Configuración y condiciones de mecanizado EDM
Para realizar el análisis se emplea una tecnología estándar de ONA para aleación de níquel, mesa giratoria de 2 ejes y dos condiciones de limpieza diferentes. Por un lado, buenas condiciones de lavado (boquillas cerradas) y, por otro lado, peores condiciones de limpieza (boquillas abiertas). Además, para el corte de desbaste se utiliza un hilo de 0.25 recubierto.
Estos dos escenarios elegidos para el estudio (boquillas abiertas y cerradas) permiten realizar diferentes pruebas para evaluar el mejor el tiempo de erosión, ya que éste depende en gran medida de las condiciones de limpieza. En ocasiones, las características geométricas de los discos de turbina impiden el uso de la electroerosión con boquillas cerradas.
Son modelos especialmente útiles para la fabricación de moldes de grandes dimensiones y distintas cavidades, justo la especialidad de Concours Mold.
\ Resultados de la investigación
Tras las pruebas realizadas, los resultados han demostrado que con la tecnología de la electroerosión por hilo es posible lograr un espesor de capa refundida en el rango de micras necesario (alrededor de 5 µm) y con suficiente precisión en las ranuras de inserción de alabes dentro de la tolerancia de 0.01 mm. Estos resultados se han obtenido después de una pasada de desbaste y dos pasadas de acabado (estrategia de 3 cortes).
En peores condiciones de limpieza (boquillas abiertas) la capacitad de arranque de material para el desbaste es de 110 mm2/ min. De hecho, para la estrategia utilizada en la investigación (una pasada en desbaste y dos pasadas de acabado), la capacidad de arranque de material es de 60 mm2/ min.
Por otro lado, en buenas condiciones de limpieza (boquillas cerradas) se observa una relevante mejora de la capacitad de arranque de material. Solo para el desbaste, alcanza más de 400 mm2/ min.
\ Comentarios basados en los resultados obtenidos
La mayor parte de los discos de la turbina tienen perfiles de ángulo entre 5 y 30 grados. La función de corte cónico de la máquina de electroerosión de hilo de ONA obtiene buenos resultados en la precisión geométrica para perfiles de menos de 10 grados. Para ángulos más grandes, se recomienda una mesa giratoria de dos ejes.
Para lograr la eliminación de material deseado y mejorar los tiempos de mecanizado es fundamental la limpieza de dieléctrico en el área de erosión. Mantener la mayoría de las boquillas cerradas en el perfil es esencial. Para discos de turbina de menor diámetro (cuando las boquillas interfieren con el dispositivo de sujeción) se recomiendan el uso de boquillas especiales.
Por último, también se recomienda el empleo de hilos recubiertos para reducir el proceso de la electroerosión por hilo, especialmente en el corte de desbaste.
\ Conclusiones
Podemos concluir, tras dicha investigación, que la electroerosión por hilo de perfiles de discos de turbina es una alternativa muy válida para competir con el brochado como solución industrial en el sector aeronáutico. Los generadores de última generación, cada vez más potentes, y los controles numéricos, más avanzados, permiten optimizar el tiempo de mecanizado y reducir el espesor de la capa blanca. Además, proporcionan una precisión geométrica muy buena.
En el estudio realizado por ONA (estrategia de 3 cortes), el mecanizado de ranuras de disco de turbina cumple con las tolerancias geométricas alcanzando una capa blanca por debajo de 5 μm. Además, se obtiene una información muy valiosa sobre la capacitad de arranque de material y el tiempo de mecanizado.
Es cierto que la certificación del proceso de mecanizado completo por electroerosión, según los estándares aeronáuticos, puede resultar un proceso largo y costoso. Por esta razón, ONA concluye que la mejor opción es combinar la electroerosión por hilo para desbaste, por ser más económico y rápido, con el brochado para el acabado final. De esta manera, no es necesaria la re-certificación del proceso.