Solución ONA para la mecanización de impellers de turbina con EDM.
\ Solución ONA para la mecanización de impellers de turbina con EDM.
Dos de las fortalezas de ONA en el sector de la fabricación de componentes de turbinas se basan en nuestro dominio del mecanizado por electroerosión (EDM) para piezas de gran complejidad, así como en nuestra experiencia de más de 25 años ofreciendo soluciones llave en mano para el sector de las turbinas.
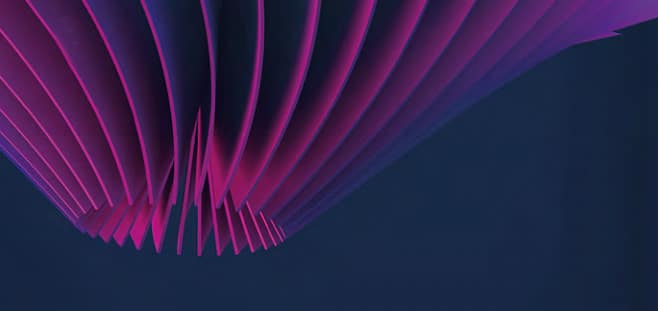
Este posicionamiento y conocimiento experto ha motivado la confianza en ONA de una de las empresas referente en fabricación de bombas y válvulas para desarrollar los impellers de las turbinas de sus equipos rotativos.
La electroerosión es la alternativa más eficiente y viable para el mecanizado de piezas con geometrías complejas, como es el caso de las cavidades de los impellers. En este sentido, la tecnología EDM, supera las dificultades presentadas por otras técnicas tradicionales, como el fresado, que puede conllevar tasas de rotura de herramientas elevadas o que, especialmente en geometrías cerradas o complejas como el caso de los impellers, no se pueda acceder con las herramientas de fresado a todas las zonas a mecanizar.
Sin embargo, y aunque el proceso de electroerosión es la vía más factible para ofrecer una solución óptima de erosión y mecanizado, esta también genera importantes retos. Exige tener en cuenta numerosos factores cuyo cálculo y definición es complicado, como el diseño y número de electrodos necesarios, su trayectoria, el nivel de desgaste…
Para dar respuesta a estos retos, nuestro equipo de ingeniería desarrolló una solución ‘llave en mano’ que cubría todas las necesidades transmitidas por el cliente. Para ello, llevó a cabo un estudio pormenorizado y valoración del caso y, posteriormente, el desarrollo con éxito de la aplicación a medida para el mecanizado de los impellers, el ‘corazón’ de las turbinas que serían utilizadas por nuestro cliente para compresores industriales
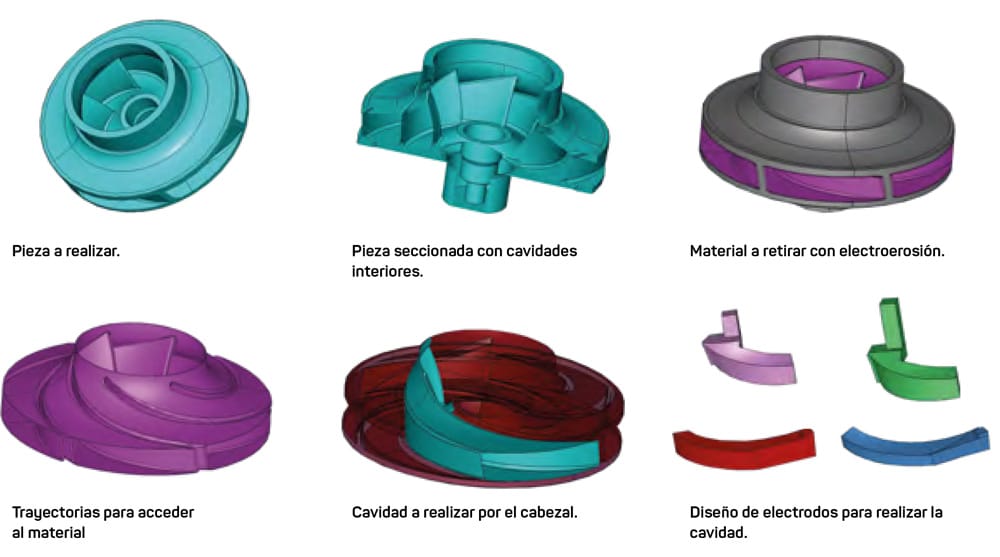
¿Cómo lo hicimos?
Partiendo de los planos facilitados por el cliente y las necesidades manifestadas, el equipo de ONA valoró la idoneidad de utilizar la tecnología de electroerosión por penetración para la ejecución de piezas con geometrías tan complejas como los impellers.
-
Layout.
En esta fase inicial, era imprescindible definir correctamente el eje involucrado en el proceso, así como la posición y orientación que debe tener la pieza de trabajo ya que, ambos factores, condicionan el diseño de los electrodos o de la trayectoria, la dimensión del mecanizado o pueden llegar, incluso, a comprometer la propia viabilidad del proyecto.
-
Diseño de electrodos y trayectoria.
En la actualidad, no existe un software comercial CAD/CAM para definir el diseño de los electrodos y trayectoria como en el caso de otras aplicaciones, sino que es necesario recurrir a conocimiento experto para desarrollar ad hoc los algoritmos y metodologías que definan estos parámetros. Esto implica que no existe una solución única, sino que cada pieza requiere de un proyecto personalizado en función de sus características y necesidades.
-
Mecanizado de los electrodos
Los retos del mecanizado y fresado de los propios electrodos tienen que ver principalmente con que se trata de geometrías complejas y que requieren tolerancias muy estrictas. Esto supone que un error en el electrodo da como resultado un error en la pieza de trabajo.
-
Parámetros de electroerosión.
Para un mecanizado estable de la pieza, es imprescindible una correcta definición de los diferentes parámetros de electroerosión. Estos parámetros vienen principalmente definidos por la rugosidad superficial requerida (a menor tiempo de mecanizado, mayor rugosidad) y la geometría (en áreas más grandes es posible aplicar mayor energía).
-
Desgaste de los electrodos.
Es una consecuencia inevitable del proceso de electroerosión que no se puede evitar, pero sí podemos llegar a controlar y minimizar.
-
Metrología
Por la complejidad de acceso de la propia pieza, el análisis dimensional de la misma es un reto en sí mismo. En este sentido, algunas de las posibilidades a barajar son el análisis destructivo, la definición de puntos estratégicos o recurrir a elementos de medición estándar.
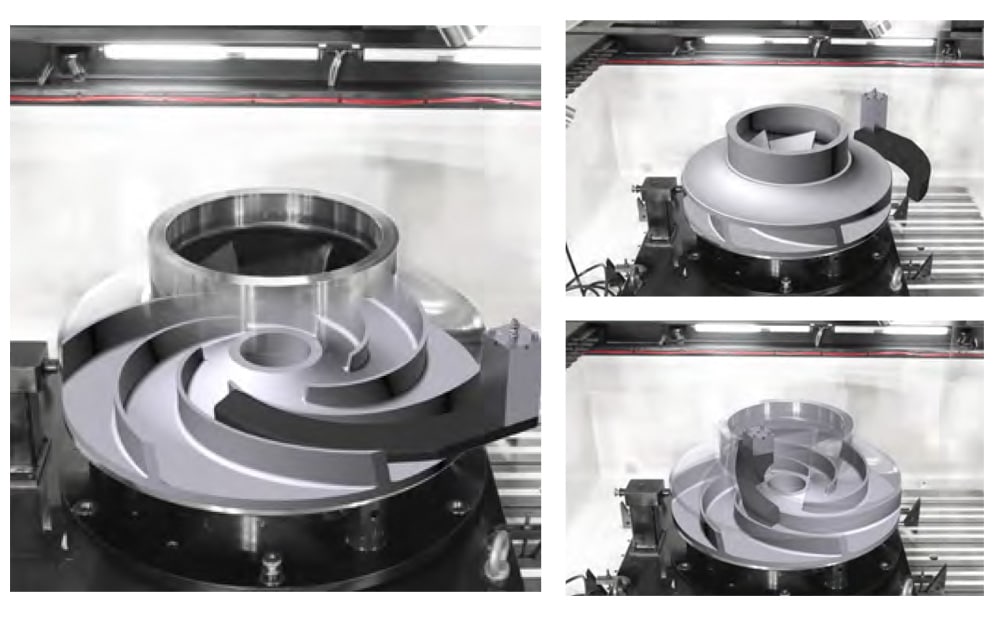
La solución de ONA: ¿Cómo se hizo?
Para superar con éxito todos los desafíos que implicaba el proyecto, un elemento imprescindible fue disponer de un equipo de ingeniería experto en tecnologías EDM como el de ONA.
Tras realizar un exhaustivo estudio previo de la pieza, los diferentes parámetros y valoración de la viabilidad del proyecto, la propuesta de nuestros ingenieros fue el desarrollo de una aplicación para nuestra máquina de electroerosión por penetración IRIS 6+. Este equipo, entre otras ventajas, aporta máxima precisión y altos niveles de productividad.
Además de la elección de la maquinaria más adecuada, en el desarrollo integral de la aplicación final realizado por ONA se establecieron parámetros críticos como, por ejemplo, la definición de los electrodos necesarios o el análisis de su desgaste. En el caso de este proyecto, la aplicación requería de 4 electrodos diferentes para conseguir las trayectorias completas. Esto supone, además, una de las ventajas competitivas de ONA por la optimización de tiempos. En cuanto al desgaste de los electrodos, si bien es imposible eliminarlo completamente, el generador 100% digital e inteligente de la tecnología ONA IRIS los reutiliza y reduce su desgaste
Igualmente, el equipo de ingenieros desarrolló la trayectoria tridimensional (curvas, inclinaciones…) que tiene que seguir nuestra máquina para que toda la ejecución sea correcta o se implementó una herramienta de fijación a medida para el correcto posicionamiento de la pieza.
Conclusiones
- ONA demuestra su capacidad para abordar proyectos integrales llave en mano.
- Desarrollo de una aplicación a medida para la fabricación de una pieza con gran complejidad por su forma, acceso y cavidades.
- Ejemplo de potencial tecnológico y especialización en electroerosión.
- Precisión y fiabilidad de las máquinas IRIS para la mecanización de piezas críticas y complejas.
- ONA como partner tecnológico especializado en sectores como la fabricación de componentes para las turbinas. En este caso concreto, enfocado en el mecanizado de impellers, pero en este número de la revista puedes leer otro case study sobre nuestra solución a medida para la realización de orifios difusores en álabes de turbinas