“Máquinas personalizadas y de alto valor para el sector aeronáutico”.
ENTREVISTA A MARIUS PETEAN, KEY ACCOUNT MANAGER DE ONA
\ “Máquinas personalizadas y de alto valor para el sector aeronáutico”.
El desarrollo de los nuevos generadores digitales inteligentes ha sido uno de los grandes impulsos para que la electroerosión se haya convertido en un proceso de fabricación viable y muy competitivo en el sector aeronáutico, incluso en las denominadas piezas criticas, es decir, rotativas o que soportan cargas cíclicas y que pueden sufrir fallos por fatiga. El papel de ONA en esta evolución tan positiva ha sido importante, con aportaciones como la máquina AV35 de corte por hilo para la fabricación de firtrees de los discos de turbina.
Tal y como señala en esta entrevista Marius Petean, Key Acount Manager de ONA, el futuro pasa por continuar apostando fuerte por un sector que ya representa el 25% del volumen anual de negocio de la compañía. “Todas las empresas importantes del sector aeronáutico utilizan máquinas ONA. El objetivo es crecer dentro de nuestros propios clientes, en las diferentes plantas que tienen distribuidas por el mundo, y también en proveedores del primer y segundo rango que utilizan máquinas de electroerosión, con un enfoque especial en el mercado de América de Norte”, destaca.
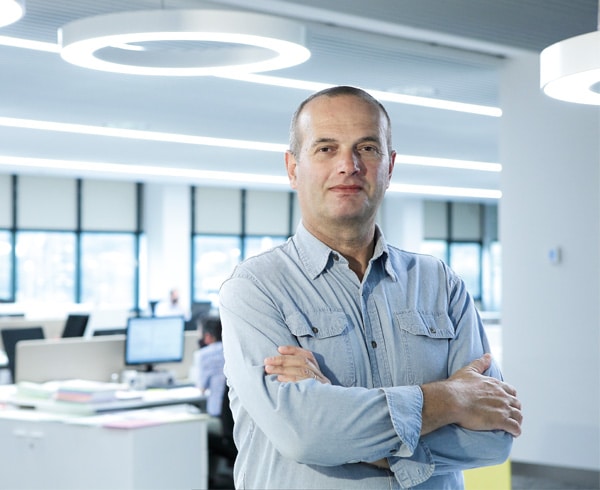
PREGUNTA. ¿Cómo se inició ONA en el desarrollo de aplicaciones para los sectores aeronáutico y de la energía?
RESPUESTA. ONA lleva involucrada más de 20 años en proyectos para el sector aeronáutico. Pero durante mucho tiempo fue dentro de un ámbito muy coyuntural. Se trataba de clientes que solicitaban máquinas que debían cumplir ciertos requisitos tecnológicos relacionados con procesos de mecanizado por electroerosión de componentes de turbina de gas. Solo hace 10 años, las ventas para empresas aeronáuticas representaban menos del 5 % de las ventas anuales de ONA. Sin embargo, no hace mucho vimos la necesidad de reenfocar la gestión de un sector que podría aumentar las ventas y, al mismo tiempo, contrarrestar y complementar a otros sectores tradicionales de negocio como moldes y matricería para automoción. Este enfoque comenzó hace 6 años. Desde entonces, las ventas de ONA en el sector aeronáutico no han dejado de crecer, llegando a representar en la actualidad el 25% de la facturación total anual, y con perspectivas de un aumento significativo en los próximos años.
P. ¿Se puede decir que la electroerosión es ya una tecnología preferente para fabricar determinadas piezas de geometría compleja en un sector tan exigente como el aeronáutico? ¿Está a la altura del brochado y el fresado en cuanto a la calidad en el producto final?
R. La electroerosión estaba considerada en la industria aeronáutica como un ‘malo necesario’. Hay ciertos componentes que se pueden mecanizar solo por electroerosión. Por esta razón, los diseñadores de piezas aeronáuticas han desarrollado procedimientos de definición de los planos de estos componentes que incluyen los requisitos del proceso de electroerosión y también los requisitos metalúrgicos y de calidad de superficie de aceptación. La electroerosión está considerada un proceso especial que tiene que ser homologado antes de aplicarlo en la producción en serie. Sin embargo, en los últimos años esta percepción está cambiando. Nuevas tecnologías de electroerosión basadas en generadores digitales de ultima generación permiten ahora, por un lado, un incremento sustancial en el arranque de material y, por otro, una mejora significativa de la calidad de superficie erosionada. La electroerosión sigue siendo el ‘malo necesario’, pero ahora está considerada una alternativa viable industrialmente para remplazar o complementar a otro tipo de mecanizados. La calidad de superficie que se puede alcanzar actualmente en electroerosión por hilo permite, por ejemplo, que este proceso sea considerado una alternativa para remplazar el brochado de los discos de turbinas.
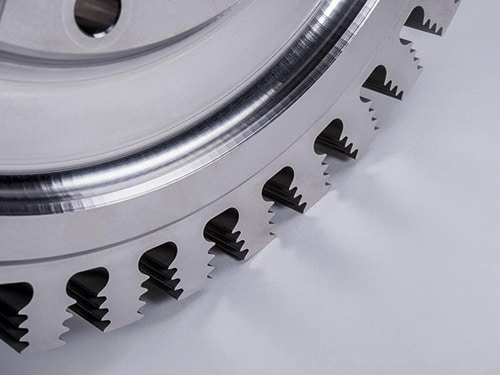
Algunos ejemplos recientes han sido la máquina ONA AV35 de corte por hilo para la fabricación de firtrees de los discos de turbina.
P. ¿De qué tipo de piezas/aplicaciones estamos hablando?
R. El abanico de aplicaciones y componentes aeronáuticos donde se aplica la electroerosión sigue creciendo. Si antes eran unas pocas aplicaciones, perteneciendo casi exclusivamente a las tradicionales de electroerosión, como las ranuras y agujeros de refrigeración en NGVs, segmentos y álabes; ahora se han diversificado, llegando a los impellers, IBRs, OGVs, discos de turbinas, cámaras de combustión o fan blades.
P. ¿A qué se ha debido este salto de los últimos años? ¿Ha sido únicamente el desarrollo de nuevos generadores lo que ha convertido a la electroerosión en una técnica de mecanizado competitiva en el sector aeronáutico, incluso en las denominadas piezas criticas?
R. Evidentemente el salto tecnológico lo han dado las nuevas generaciones de generadores, pero también los avances de desarrollo de tecnología de electroerosión. Si antes se podían configurar solo unos cuantos parámetros de electroerosión, ahora se está trabajando con más de 30 parámetros configurables. Esto permite mucha más flexibilidad a la hora de encontrar una solución óptima. Luego, para que se haya podido introducir la electroerosión en piezas críticas, hay que reconocer la labor de los OEMs, la voluntad y la tenacidad de sus responsables de ingeniería y de fabricación, que han estado abiertos y preparados para aceptar, validar y homologar la electroerosión en ese tipo de piezas. Sin ellos, llegar a este punto no habría sido posible.
P. ¿Qué ventajas técnicas han traído los nuevos generadores para la fabricación con electroerosión de, por ejemplo, discos de turbinas de gas, piezas rotativas que alcanzan hasta las 60.000 revoluciones por minuto y que deben estar preparadas para resistir temperaturas y fluctuaciones de presión extremas?
R. En el caso de los nuevos generadores de ONA, ha sido el hecho de que sean digitales. Se pueden programar tecnologías que permiten eliminar la electrolisis y las micro-fisuras, alcanzando niveles muy bajos de capa refundida, de tan solo unas micras. Los requisitos de superficie son aceptables y las piezas pueden ser homologadas para volar.
P. ¿Qué ventajas ofrece la electroerosión en la fabricación de piezas para el sector aeronáutico respecto a técnicas más tradicionales como el brochado y el fresado?
R. Desde el punto de vista industrial, se han perfilado unas ventajas muy interesantes sobre todo en la electroerosión por hilo. El coste de consumibles, comparado con el mecanizado convencional de fresado y brochado, es significativamente menor. En el caso del brochado, la electroerosión por hilo ofrece soluciones de prototipaje rápidas y baratas. Una herramienta de brochado, entre diseño y fabricación, puede requerir de hasta un año, mientras que para la electroerosión por hilo es algo casi inmediato, siendo relacionado directamente a la programación de corte de perfil. Además, esta aproximación no permite errores; si la herramienta de brochado por alguna razón no es la adecuada, se tiene que repetir y realizar las modificaciones para obtener una nueva. ¿¡Otro año!? En el caso de la electroerosión, después de cortar la figura en la pieza, se mide el perfil y si hay que ajustar, se ajusta directamente en la programación de trayectoria de corte. Por otro lado, la autonomía de la máquina de electroerosión por hilo es otra ventaja importante. Todos los modelos AV de ONA tienen la opción de utilizar un sistema de bobina de hilo de 45 kg., casi 8 veces más que una bobina estándar de 8 kg. Y en lo que respecta a la electroerosión por penetración, se nota una tendencia hacia la automatización con robots y almacenes individuales o compartidos de electrodos.
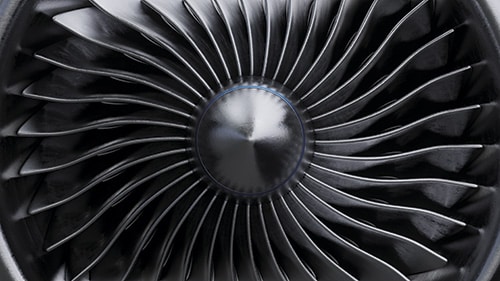
P. ¿Los métodos de mecanizado tradicionales tienen limitaciones que no tiene la electroerosión a la hora de conseguir ciertas geometrías o trabajar con ciertos materiales?
R. La electroerosión es un proceso de mecanizado sin contacto. Solo se necesita que los materiales a erosionar tengan conductividad eléctrica. Obviamente esto es una ventaja sobre el mecanizado convencional. No hay casi diferencia entre el arranque de material y desgaste de herramienta (electrodo) si se erosiona aluminio o aleaciones de níquel, lo que en el mecanizado convencional es desigual.
P. ¿Qué papel ha jugado ONA en esta evolución que ha convertido a la electroerosión en una técnica preferente para la fabricación de piezas aeronáuticas?
R. Trabajamos con nuestros clientes para buscar soluciones de mecanizado especificas para sus componentes. Buscamos soluciones para sus problemas utilizando siempre la electroerosión. Digamos que de estos ejercicios salen soluciones interesantes y muchas veces sorprendentes.
P. ONA fabrica, por tanto, soluciones personalizadas o customizadas para las empresas del sector.
R. Absolutamente. Nuestra estrategia en el sector es proporcionar a los clientes soluciones con alto valor añadido. Les escuchamos y les ofrecemos soluciones personalizadas según sus requisitos y su nivel de conocimiento en electroerosión. Por poner un ejemplo: un cliente con poca experiencia en EDM que nos pida una solución llave en mano que incluya diseño y fabricación de utillajes, programación CN y tecnología de electroerosión y validación industrial de piezas. Dos referencias diferentes y, en total, nueve operaciones distintas EDM.
P. ¿Cuáles han sido las últimas aportaciones/aplicaciones tecnológicas de ONA para el sector aeronáutico?
R. Algunos ejemplos recientes han sido la máquina ONA AV35 de corte por hilo para la fabricación de firtrees de los discos de turbina; las máquinas de electroerosión por hilo para el corte de forma automatizada de perfiles aerodinámicos para el encaje de álabes en anillas verticales; la electroerosión por penetración con alto rendimiento de arranque de material; la electroerosión por penetración adaptada para cavidades complejas en componentes tipo impeller; o la electroerosión por penetración de agujeros con forma en álabes y NGVs.
P. Decía que el 25% de las ventas anuales de ONA se producen ya en el sector aeronáutico, pero ¿qué previsiones manejan para el futuro?
R. Todas las empresas importantes del sector aeronáutico utilizan máquinas ONA. Nuestro objetivo es crecer dentro de nuestros propios clientes, en las diferentes plantas que tienen distribuidas por el mundo, y también en proveedores del primer y segundo rango que utilizan máquinas de electroerosión, con un enfoque especial en el mercado aeronáutico de América de Norte.
P. ¿Por dónde irán las próximas innovaciones en maquinaria de electroerosión para el sector? ¿Cuáles serán los próximos retos para demostrar que la electroerosión es una tecnología más viva que nunca para la fabricación de piezas aeronáuticas?
R. Se está innovando constantemente en tecnología y en procesos. Aparecen nuevas aplicaciones para electroerosión según el desarrollo y la introducción de nuevas tecnologías. Un ejemplo revelador es la electroerosión para cortar piezas elaboradas por fabricación aditiva. En el futuro se necesitarán no solo tecnologías adaptadas, sino también máquinas diferentes mejor adecuadas a la tipología y el tamaño de las piezas de fabricación aditivas. Un mayor reto será la ciberseguridad de las máquinas dentro de un ámbito industrial digital y conectado. Y un valor añadido importante para los clientes/usuarios de máquinas de electroerosión será la recopilación de datos de máquina y del proceso para su análisis con el fin de mejorar los procesos y el mantenimiento preventive.